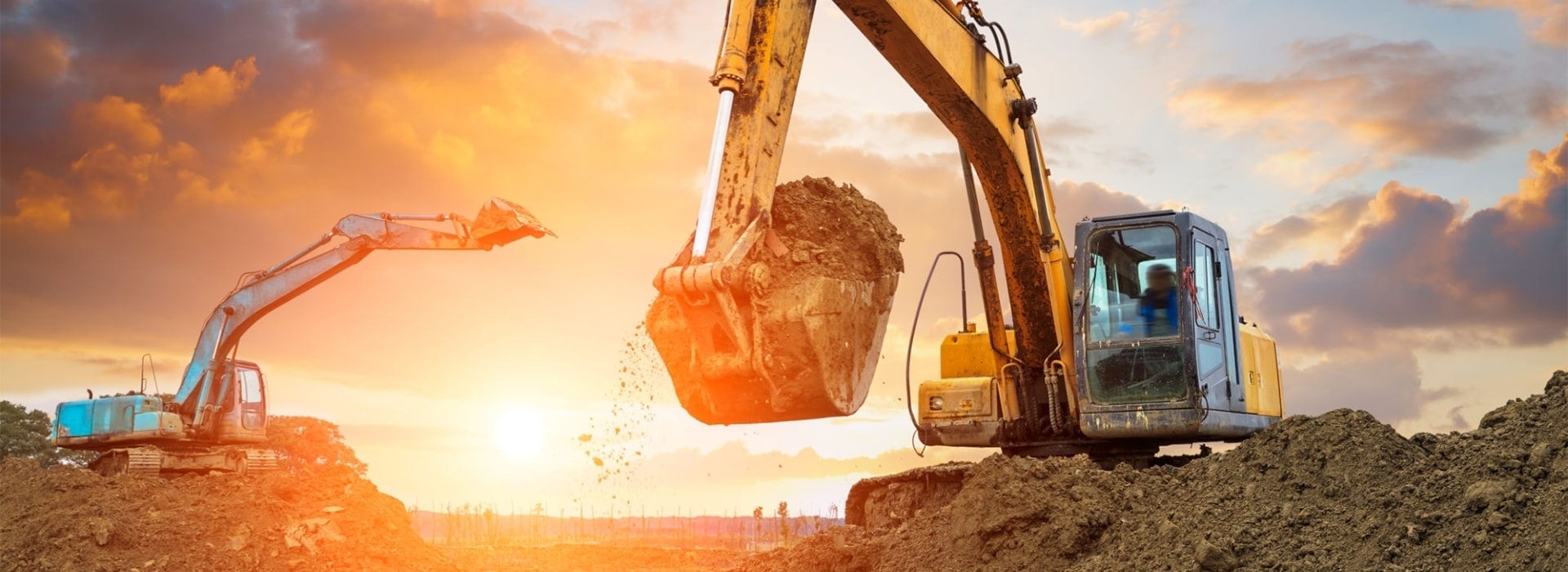
Customized 35CrMo forged steel segmented large diameter ring gear
PRODUCT PARAMETERS
Description
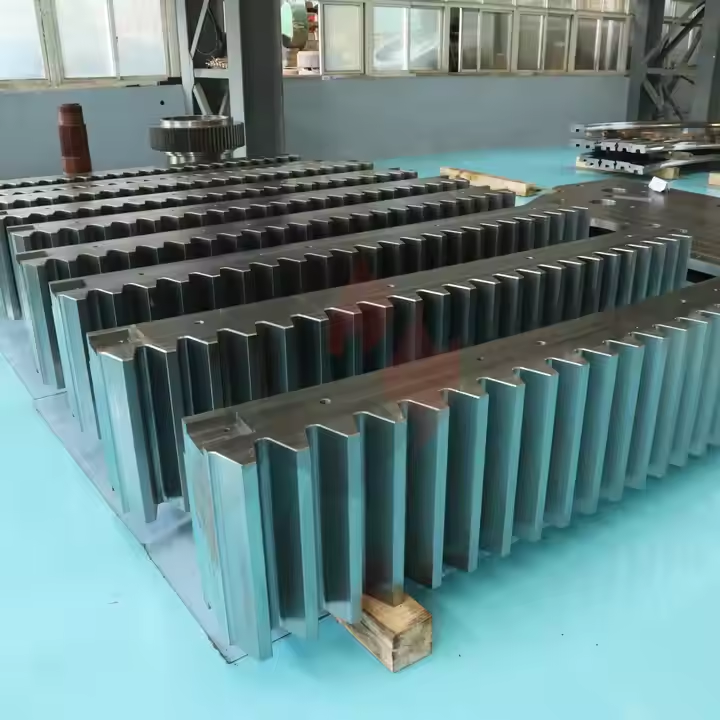
1 Overview of segmented ring gear
The segmented ring gearis a transmission component specially designed for large mechanical equipment such as rotary kilns, ball mills, etc. It simplifies the installation and maintenance process by dividing the entire ring gear into several segments. Each segment is independently manufactured with high strength and wear resistance, and can withstand large loads and complex working conditions. This design is not only convenient for transportation and assembly, but also only replaces the damaged part when worn or damaged, reducing maintenance costs and extending the service life of the equipment. In addition, the design of the segmented gear ring optimizes the mechanical transmission efficiency and improves the overall performance of the equipment.
Parameter Table
Material: | Carbon steel, alloy steel |
Gear module: | 8-200 |
Structure: | Forging |
Gear length: | Maximum 10,000 mm |
Standard: | ASTM DIN, EN GOST JIS, etc. |
service: | Based on customer drawings |
Heat treatment: | Q&A |
- Application of segmented ring gear
We can produce large forging,casting and welding gears according to customer’s drawings.According to the working conditions and clients’ request,we also can do gear grinding,surface hardening,cemented and quenching,Nitriding and quenching,etc.
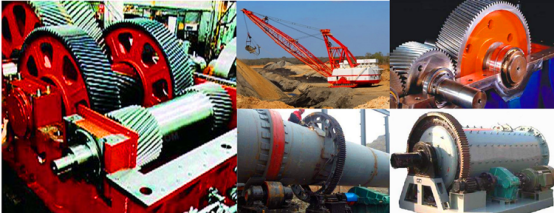
Our large diameter spur ring gear segment large ring gear mainly used for Rotary kiln,Ball Mill,Dryer,etc.
3. Segmented gear ring production process
-Forging
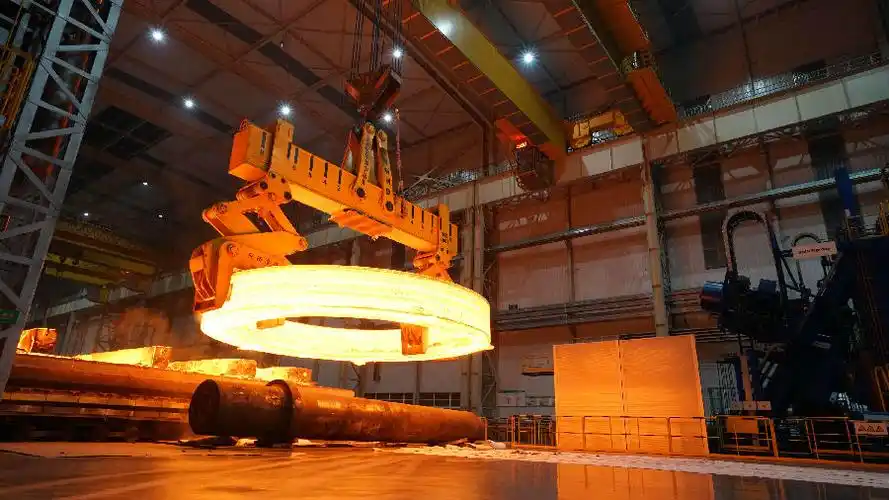
The steel is initially formed by die or free forging to obtain a rough gear ring shape.
– Heat treatment
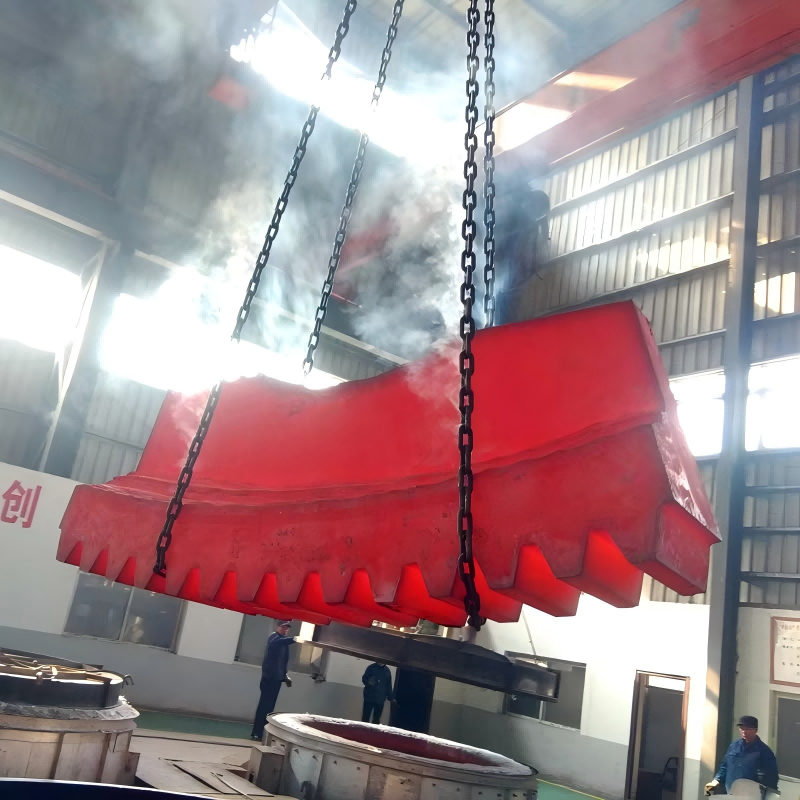
After preliminary mechanical processing, in order to improve the comprehensive mechanical properties (strength, hardness, toughness) of the material, a quenching and high-temperature tempering quenching treatment is required.
-Machining
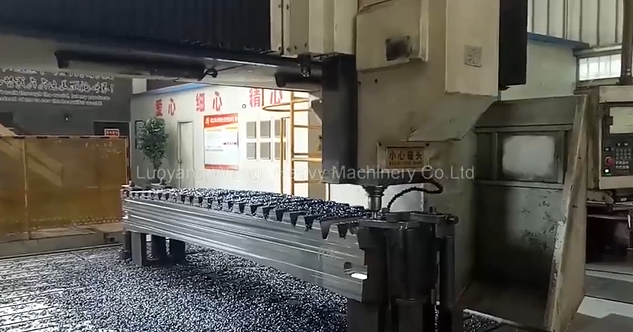
Rough turning: Use CNC lathe to perform preliminary turning on the forging to form the basic geometric shape.
Fine turning: Further turning to achieve more precise size and surface finish.
-Inspection and testing
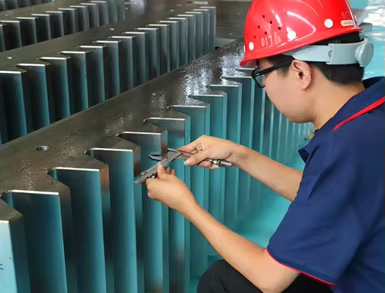
Dimension detection: Use three-coordinate measuring machine, gear measuring instrument and other equipment to check key size and shape tolerance.
Non-destructive testing: Such as magnetic particle testing, ultrasonic testing, etc., to ensure that there are no cracks or other defects inside.
Performance testing: Hardness testing, tensile testing, etc. are carried out as needed to verify the mechanical properties of the material.
– packaging
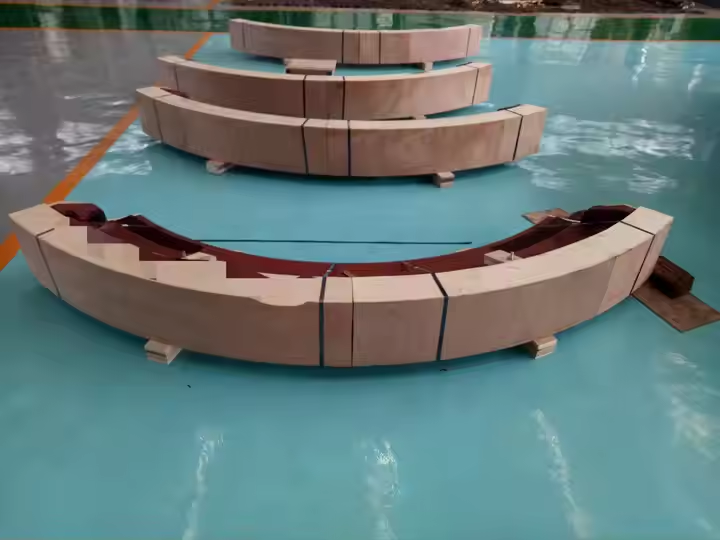
Assembly: If necessary, assemble the processed segmented gear ring with other components into a complete rotary mechanism.
Packaging: Finally, clean and rust-proof treatment is carried out, and it is protected with appropriate packaging materials for transportation and storage.
5.Why Choose Us
– 40+ years experiences focus on metal research and mining machinery spare parts.
– Three international key projects, such as Segment girth gear used in the Suez Canal in Egypt
– Besides five workshops, 100+ sets of equipment, capablity of integrating equipment resources from 300+ enterprises (suppliers)
-8 material senior engineers and 40+ patents
REQUEST A QUOTE
RELATED PRODUCTS
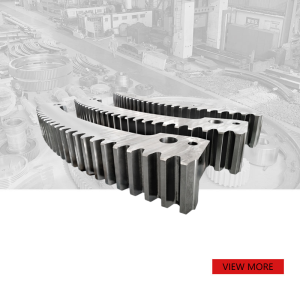
35CrMo Forging Mining large dimeter 12 Segment Arc Tooth
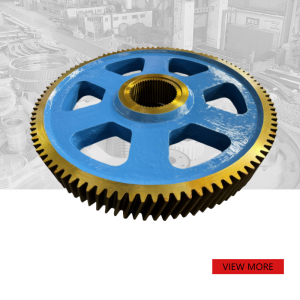
High quality casting large helical gear wheel
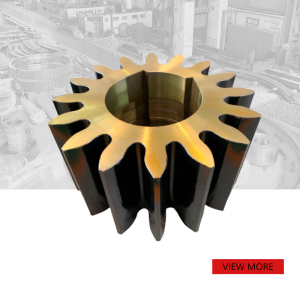
Custom sugar mill pinion forging large gear
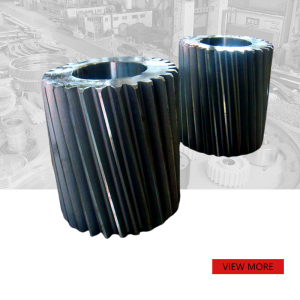
Forging AISI4140 non-standard large Helical gear for ball mill
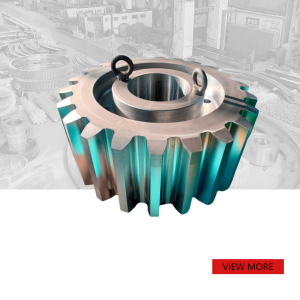
Forging cuatomized 42CrMo large module mining machinery Spur Gear
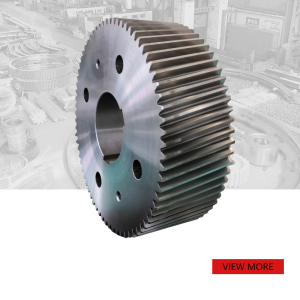